CNC Lathe Part Factories: The Backbone of Precision Manufacturing
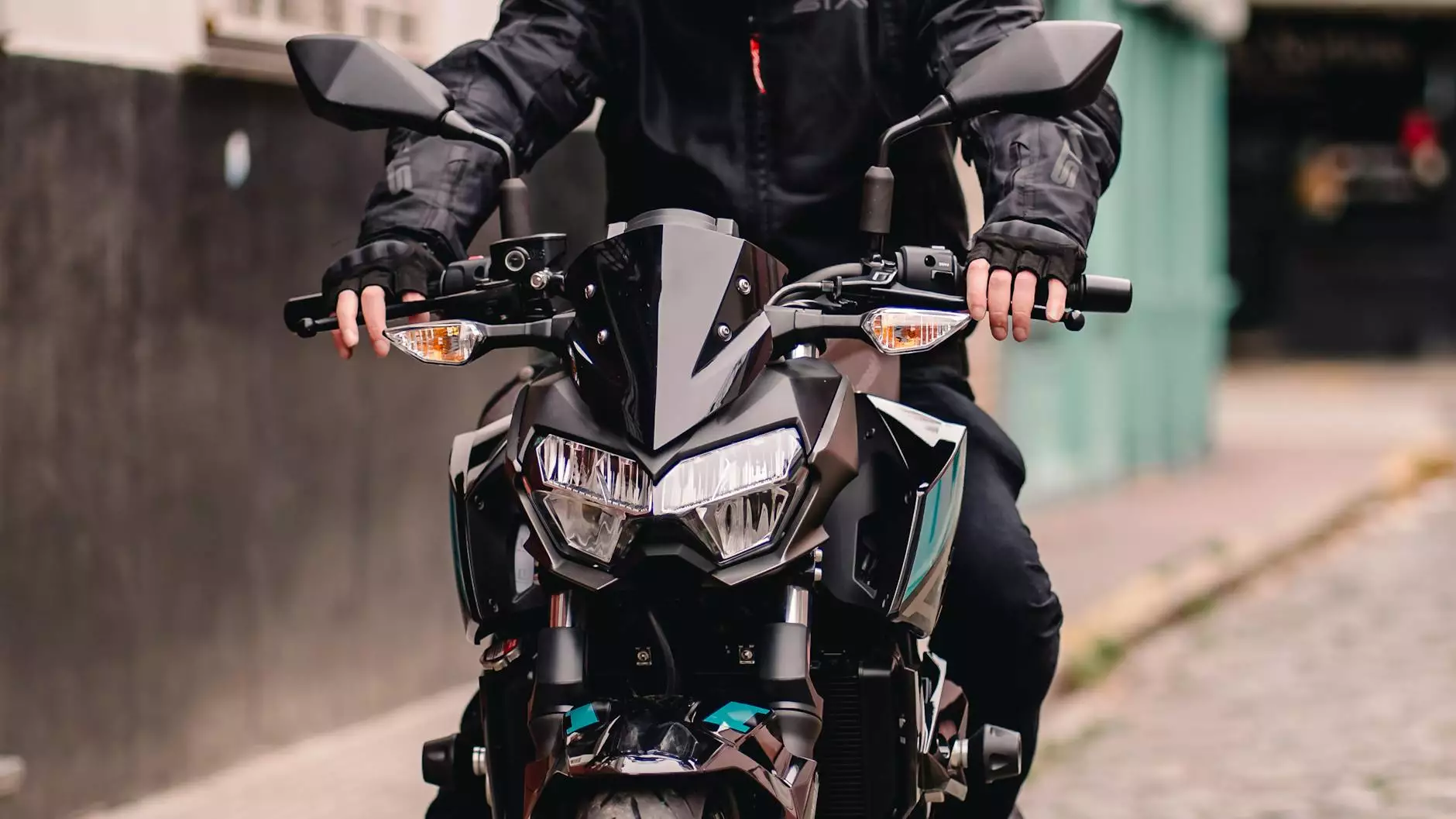
In today's fast-paced industrial landscape, the demand for precision and quality in manufacturing has reached unprecedented heights. CNC lathe part factories play a critical role in meeting these demands, offering advanced solutions for producing components used in a wide range of applications. This article delves into the significance of CNC lathe technology, the processes involved, and how these factories contribute to the metal fabrication industry.
Understanding CNC Lathe Technology
CNC, or Computer Numerical Control, refers to the automated control of machining tools through a computer. In the context of lathe machines, this technology allows for the precise shaping and cutting of materials, including metals such as aluminum, steel, and titanium. Unlike traditional lathes operated by hand, CNC lathes enhance productivity and accuracy through programmable software. With the ability to produce intricate designs and features, CNC lathes are indispensable in modern manufacturing.
The Evolution of CNC Lathe Machines
The history of lathe technology dates back thousands of years; however, the CNC revolution reshaped the manufacturing landscape. Here are some key milestones:
- Early Lathes: Originating in ancient Egypt, these manual devices were used for shaping wood and metal.
- Introduction of Electricity: The 19th century saw the introduction of electric motors, paving the way for more efficient lathes.
- Development of CNC Technology: In the 1940s and 50s, numerical control systems were developed, leading to the automated machines of today.
- Integration of Computer Technology: The late 20th century witnessed the integration of computers into CNC systems, enabling enhanced control and precision.
The Importance of CNC Lathe Part Factories
CNC lathe part factories are vital in sectors ranging from aerospace and automotive to medical and electronics. Their ability to produce precise components efficiently addresses various industry needs. Let's explore some of the key benefits of these factories:
1. Unmatched Precision
Precision is paramount in manufacturing, especially in industries where tolerances are critical. CNC lathes can produce parts with tolerances as tight as ±0.001 inches. This level of precision leads to:
- Improved product quality and reliability
- Reduced waste and production costs
- Enhanced performance of assembled components
2. Increased Efficiency
CNC machines operate continuously and can run unattended for long periods, significantly increasing productivity. This efficiency results in:
- Shorter lead times for production
- The ability to handle complex projects with ease
- Rapid scaling of production based on demand
3. Versatility in Material Use
One of the standout features of CNC lathe part factories is their ability to work with a diverse set of materials. From high-strength alloys to soft plastics, the capability to switch between different materials expands potential applications. The versatility offers:
- Customization options tailored to specific client needs
- The ability to innovate with new materials and designs
- Support for a broad spectrum of industries
Key Processes in CNC Lathe Part Factories
Understanding the processes that take place in CNC lathe part factories can shed light on how raw materials are transformed into high-quality components. Here are the core steps:
1. Design and Prototyping
The first step in the CNC manufacturing process is the design phase, which involves creating detailed drawings and specifications. This is typically done using Computer-Aided Design (CAD) software. Once the design is finalized, a prototype may be created to test functionality and fit.
2. CAM Programming
After the design stage, the next step is creating a Computer-Aided Manufacturing (CAM) file. The CAM software translates the CAD design into a language that the CNC machine can understand, detailing the precise movements and tooling required for production.
3. Machine Setup
During machine setup, operators prepare the CNC lathe for production. This involves selecting the appropriate tooling, clamping the workpiece securely, and inputting the CAM file into the machine’s control system.
4. Machining Process
With everything set up, the CNC lathe begins the machining process. The machine follows the programmed instructions, performing cutting, drilling, and shaping operations on the material with remarkable accuracy. Throughout this phase, operators monitor the process to ensure all parameters are adhered to, verifying the quality of the output.
5. Quality Control
Once the components are manufactured, rigorous quality control measures are implemented. This may include:
- Dimensional inspections using precision measuring tools
- Testing for material integrity and surface finishes
- Ensuring compliance with industry standards
The Role of DeepMould.net in CNC Lathe Part Manufacturing
As a notable player in the field, DeepMould.net offers exceptional services in CNC machining and metal fabrication. Their commitment to quality and precision makes them a trusted partner for a variety of industries. Here’s how they maintain their competitive edge:
1. Advanced Technology and Equipment
DeepMould.net continually invests in state-of-the-art CNC lathe machinery, enabling them to produce complex parts with unparalleled quality. Their equipment features:
- High-speed spindles for increased efficiency
- Multi-axis capabilities for intricate designs
- Automation systems to streamline production
2. Highly Skilled Workforce
The factory employs a team of skilled engineers and technicians who are well-versed in CNC technology. Their expertise ensures that each project is handled with the utmost care, guaranteeing the best possible outcomes.
3. Comprehensive Services
In addition to manufacturing, DeepMould.net offers a range of services, including:
- Consultation on design for manufacturability
- Prototyping services to validate designs
- Post-production services like finishing and assembly
Future Trends in CNC Lathe Part Factories
The landscape of CNC lathe part manufacturing is ever-evolving. Here are some prominent trends shaping the future:
1. Automation and AI Integration
As technology advances, automation and Artificial Intelligence (AI) will play an increasingly significant role in manufacturing processes. Factories will adopt smart technologies to enhance efficiency, reduce downtime, and optimize production schedules.
2. Sustainable Manufacturing Practices
With growing awareness of environmental issues, sustainable practices are becoming a priority. Factories are employing techniques that minimize waste and energy consumption, improving their overall carbon footprint.
3. Customization and Rapid Prototyping
As customer demand shifts towards personalized products, CNC lathe part factories will focus on offering customization services. Rapid prototyping will enable clients to receive tailored components quickly and efficiently, meeting specific needs in real-time.
Conclusion: The Enduring Legacy of CNC Lathe Part Factories
In conclusion, CNC lathe part factories represent a pivotal component of modern metal fabrication and manufacturing. Their ability to produce high-quality, precise parts across various industries will continue to drive innovation and progress. As technologies evolve and industries grow, so too will the importance of CNC lathe factories in ensuring that businesses meet the demands of the future.